Elettrolaser lasers are designed to help companies optimize their processes and facilitate the work of operators, allowing them to easily achieve aesthetically and functionally perfect welds on a large quantity of different metals, both precious and non-precious. To provide concrete support to companies in this sense, Elettrolaser has equipped its machines with a user-friendly user interface that simplifies the laser beam setting.
The presence of such an interface, which facilitates communication between the user and the laser, not only improves companies' performance and reduces the learning time necessary for operators to become independent in using the welder but also contributes to the transformation of companies towards the Industry 4.0 perspective, allowing our customers to take advantage of incentive to support production realities that invest in digitization and automation of their processes.
Configurable parameters through the control panel of Elettrolaser welders
The control panel of Elettrolaser welders allows for easy setting of the various parameters that regulate the emission of the laser beam, modifying them according to the type of processing that needs to be carried out.
The calibration of the different parameters allows for optimal results to be obtained, regardless of the type of metal being worked on, its thickness, and its shape.
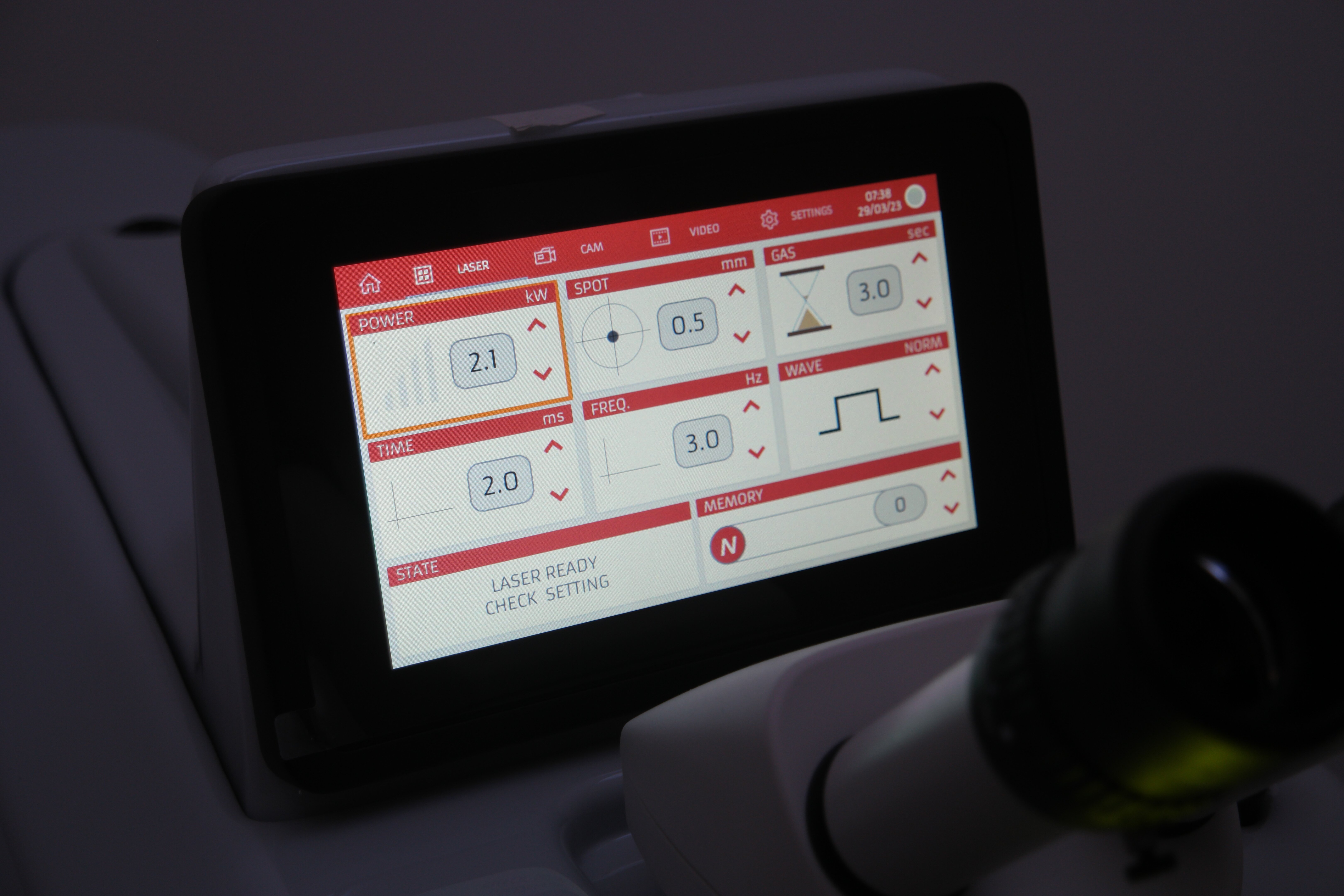
The interface integrated into Elettrolaser welders allows for the adjustment of six different parameters:
- Power: the power adjustment determines how much force the laser beam will exert on the metal to cause fusion, without burning it.
- Time: the "time" parameter allows the duration of the laser beam to be adjusted, measured in milliseconds. The combination of time and power determines how deeply the beam will penetrate the metal and how high the temperature variation will be in the area of metal that is hit.
- Spot: this parameter is used to determine the diameter of the firing point, and therefore the working area on which the laser beam will act. Since a larger spot determines a lower concentration of energy, larger spots are used to complete tasks that do not require reaching high depths (such as reducing porosity), while smaller spots are used to involve the entire thickness of the object being treated.
- Frequency:
the frequency indicates how many shots are fired in one second if the operator holds down the firing command pedal. This parameter can vary depending on the type of intervention that needs to be carried out, as well as the operator's experience.
- Wave: by intervening on this parameter, it is possible to modify the distribution of power in the established firing time. The machine can be set to deliver full power throughout the "time" parameter, or to increase or decrease that power over time. It is therefore possible, for example, to make the machine deliver minimum power at the beginning of firing, which increases to touch the maximum power defined only at the end of the expected firing interval.
- Gas: to weld some materials, such as titanium, it is necessary to use Argon gas, which is delivered according to precise criteria. The gas leakage, in fact, begins before the actual welding process starts and continues even after the work is completed. The control panel allows the emission duration of the gas to be set, so that it is known how long it will continue to leak after the last shot.
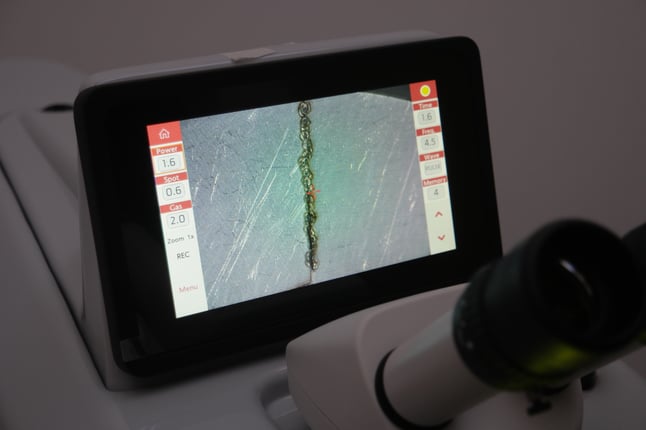
All the advantages of the Elettrolaser user interface
The parameters that regulate the emission of a laser beam are many and need to be controlled precisely to obtain satisfactory results, and the Elettrolaser user interface makes it easy to do so, regardless of the type of material to be welded.
Moreover, through the control panel of the welder, it is possible to:
- Access a library of predefined configurations for various parameters, to quickly set up the machine according to the material to be processed and the type of processing to be carried out. Each welder is capable of storing up to 100 different configurations, which can be defined at the time of machine commissioning or added autonomously later on, directly by the operator.
- Create customized profiles for each operator who uses the machine.
- View the working area during welding through a dedicated integrated camera.
- View video tutorials that illustrate how to perform some routine maintenance and cleaning operations on the machine.
- Receive alerts that signal any anomalies in the laser's operation, to intervene promptly in case of unexpected events.
Finally, the ability to easily set the parameters that regulate the emission of the laser beam allows for a drastic reduction in the time required for operator training. In just a few hours, operators can become completely autonomous in using the welder.
When a laser is commissioned at a customer's company, Elettrolaser always offers operator training services and remains available to carry out any subsequent re-training interventions in case of personnel turnover or emerging new needs. These training activities usually take place within a few hours, and within a day, all collaborators are normally able to use the laser completely independently.
Do you want to know more about the Elettrolaser catalog and the features of our welder interfaces? Contact us!
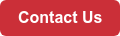