One of the great advantages associated with the use of a welding machine or a laser marking machine is the possibility of using a high-performance tool, simple to use and very convenient from the point of view of management and maintenance costs.
In fact, laser marking and welding machines consume a small amount of energy and do not generally require periodic interventions for the replacement of components or for the integration of consumables. For the machine to operate efficiently over time, it is sufficient to regularly provide for its ordinary cleaning (particularly important in the case of laser markers, which produce metal residues that must be periodically removed) and provide for scheduled extraordinary maintenance interventions aimed at carrying out a more thorough cleaning of the instrument and to check the correct functioning of all its components.
The frequency of extraordinary maintenance varies according to the type of instrument installed, the environment in which the machine operates and its intensity of use. However, Elettrolaser remains available to intervene, on request, at any time, to provide a truly efficient and timely service.
Customer support and request for components
Elettrolaser is always available to its customers to provide assistance. In case of need, customers can easily contact our technicians - by phone or by message - by referring to a specific WhatsApp number that is communicated to them when the machine is supplied.
In this way, if any problem occurs, the customer has the opportunity to communicate directly with the company, to analyze the criticality and possibly agree on an intervention on site or the dispatch of the necessary spare parts - which are provided free of charge if the laser is still under warranty - to restore machine functionality.
Shipping of spare parts and delivery times
In the event that it is necessary to intervene on the laser to replace a piece, our technicians are able to complete the repair in a short time, also thanks to the almost immediate availability of almost all the machine components. Except for some more delicate parts - which can take a few days to be tested - almost all the parts can be replaced quickly and directly by our technician who intervenes on the customer's premises, without the need to call in external intermediaries or to order spare parts from others providers. This operating mode significantly reduces the waste of time and allows us to provide the customer with a timely service, which allows him to return to operation as soon as possible.
Scheduled maintenance interventions
If our customers, for internal organizational reasons, prefer to agree in advance a scheduled maintenance schedule, Elettrolaser is at their disposal to provide this type of service. This choice, however, remains completely optional: each customer can decide whether to schedule maintenance interventions on a regular basis or whether to contact us only in case of need, according to his needs. In both cases, our technicians are able to intervene - in person or, if this is not possible, remotely - in a timely manner, providing all the materials necessary to complete the repair and put the laser back into operation.
To find out more about the offer of spare parts and the supply of Elettrolaser consumables, contact us now!
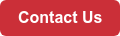